The global electric vehicle (EV) market is growing at a breakneck pace. Amid fierce competition and technological innovation, one company consistently stands out — BYD. Short for “Build Your Dreams,” BYD has transformed itself from a small battery manufacturer into one of the world’s leading EV producers. But what’s the secret behind BYD’s meteoric rise?
The answer lies in its strategic approach to vertical integration. Unlike many automakers that rely on third-party suppliers, BYD controls nearly every component of its manufacturing process. From battery production to semiconductors and final vehicle assembly, BYD’s in-house model enables it to innovate faster, reduce costs, and scale more efficiently than its rivals.
In this blog post, we’ll explore how BYD’s vertically integrated production model helps it lead the EV revolution. We’ll also discuss the challenges it faces, the implications for the global auto industry, and why investors, analysts, and consumers should keep a close eye on this Chinese powerhouse.
The Humble Beginnings of BYD
Before diving into its EV strategy, it’s important to understand BYD’s origins. The company was founded in 1995 by entrepreneur Wang Chuanfu in Shenzhen, China. Initially focused on rechargeable batteries for mobile phones, BYD quickly became a top supplier to global brands like Nokia and Motorola.
In 2003, BYD made a bold move by acquiring a struggling car manufacturer, Xi’an Qinchuan Automobile Company. This marked the company’s entry into the automotive sector. Many were skeptical at the time — what did a battery maker know about building cars? But BYD saw something others didn’t: the future of cars was electric.
Fast-forward two decades, and BYD is now a global EV juggernaut, producing not only passenger vehicles but also electric buses, trucks, and monorails. In 2023, BYD overtook Tesla in global EV sales, cementing its position as a dominant force in the clean energy transition.
What is Vertical Integration, and Why Does It Matter?
Vertical integration is a business strategy where a company controls multiple stages of its supply chain. In the automotive world, this means owning the production of critical components — batteries, chips, electric motors, software — and assembling the final vehicle in-house.
For BYD, this model provides several competitive advantages:
- Cost Control: BYD avoids supplier markups and can optimize production costs.
- Quality Assurance: With tighter control over components, BYD ensures high product reliability.
- Supply Chain Stability: In-house production shields BYD from global disruptions like chip shortages.
- Innovation Speed: Engineers can collaborate across departments, accelerating R&D.
- Scalability: BYD can ramp up production quickly without waiting on external partners.
This approach contrasts sharply with companies like Tesla, which outsources many of its parts, and traditional automakers who rely on legacy supply chains that are less agile.
BYD’s EV Supply Chain: Built from the Ground Up
Battery Production: The Core of the EV
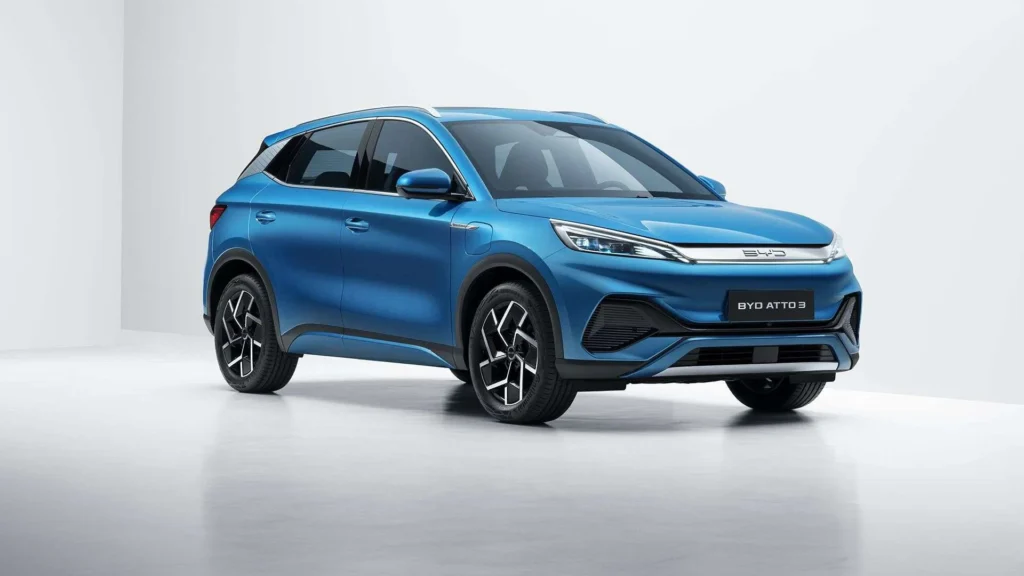
The battery is the heart of every EV, and BYD has long recognized its strategic importance. As one of the world’s largest battery manufacturers, BYD produces its own lithium iron phosphate (LFP) batteries under the “Blade Battery” brand.
The Blade Battery has gained attention for its high safety standards, long life cycle, and impressive energy density. Unlike traditional lithium-ion batteries, LFP batteries are more stable and less prone to catching fire — a critical feature for EVs.
Because BYD manufactures these batteries in-house, it avoids the high costs and supply constraints faced by other automakers relying on external battery providers like CATL, LG Energy Solution, or Panasonic.
Semiconductors and Chips: BYD’s Response to Global Shortages
The COVID-19 pandemic exposed a critical vulnerability in the auto industry: chip shortages. As vehicles became more reliant on software and electronics, automakers scrambled to secure microchips. BYD, however, sidestepped much of this chaos.
Thanks to its acquisition of chipmaker Nexperia and its in-house semiconductor division, BYD can produce many of the microcontrollers and power electronics needed for its EVs. This integration proved to be a game-changer in maintaining production volume while competitors had to pause or scale back.
EV Motors and Power Electronics: All Under One Roof
From induction motors to permanent magnet synchronous motors, BYD manufactures all key powertrain components internally. The company also builds its own motor control units (MCUs), inverters, and onboard chargers.
By doing so, BYD not only ensures part compatibility but also reduces delays and system inefficiencies that come from using multiple suppliers. This level of precision boosts performance, increases reliability, and allows BYD to tailor the driving experience to each vehicle platform.
Vehicle Assembly and Design
BYD designs, tests, and assembles all its vehicles in proprietary facilities. This includes the popular BYD Han, Tang, Dolphin, and Seal models. Because the company manages everything from frame to firmware, it can optimize design decisions without compromise.
The results are evident in vehicle quality and cost-effectiveness. For example, the BYD Dolphin — a compact hatchback — is priced aggressively while still offering advanced features like smart connectivity, high-end interiors, and competitive range.
BYD’s Global Expansion Strategy
As the EV market matures, BYD is eyeing international markets. In recent years, the company has expanded aggressively into Europe, Southeast Asia, Australia, and Latin America. It has even entered Japan — a notoriously difficult market for foreign automakers.
BYD’s vertical integration gives it a strategic edge in these markets. By controlling production costs, it can offer competitive pricing. It also means fewer compatibility issues and faster adaptation to local regulations and preferences.
BYD in Europe
Europe is rapidly phasing out internal combustion engine (ICE) vehicles. This presents a golden opportunity for EV makers. BYD has launched models like the Atto 3 and Tang EV in countries like Norway, Germany, and the UK, often undercutting competitors in price while matching them in performance.
The company has also invested in local partnerships and plans to open manufacturing facilities in Europe to bypass tariffs and import restrictions.
BYD in Latin America and Southeast Asia
In emerging markets, affordability is key. BYD’s control over the supply chain allows it to offer budget-friendly EVs without sacrificing quality. In Brazil, Chile, Thailand, and India, BYD has rolled out electric buses and cars that appeal to both consumers and governments focused on reducing pollution.
Comparing BYD with Tesla: A Tale of Two Titans
Tesla and BYD are often compared in the EV world, but their approaches differ dramatically. Tesla excels in branding, user experience, and autonomous technology. BYD, on the other hand, thrives in manufacturing efficiency, supply chain control, and affordability.
While Tesla relies on partners like Panasonic for batteries and TSMC for chips, BYD builds these components itself. This has allowed BYD to scale faster in recent years and weather supply shocks more effectively.
In 2023, BYD overtook Tesla in quarterly EV deliveries. While Tesla remains dominant in premium markets like the U.S., BYD is winning the volume game globally.
Challenges and Risks in BYD’s Path
While BYD’s vertical integration has propelled it to the forefront of the EV industry, it also comes with challenges:
- High Capital Costs: Building factories, chip fabs, and battery plants requires significant upfront investment.
- Complex Management: Coordinating diverse operations under one roof can strain resources and leadership.
- Geopolitical Risks: As a Chinese company, BYD faces scrutiny and potential trade barriers in markets wary of foreign influence.
- Innovation Pressure: Being self-reliant means BYD must stay ahead in all technologies — from AI software to battery chemistry — or risk falling behind.
Nonetheless, BYD has so far managed these risks effectively, positioning itself as a resilient and agile player in the EV arena.
What It Means for the Future of the EV Industry
BYD’s success has forced the global auto industry to reconsider how vehicles are made. Automakers that previously depended on sprawling supplier networks are now exploring vertical integration themselves.
For example:
- Ford is investing in its own battery plants with SK Innovation.
- Volkswagen has launched its PowerCo battery unit to internalize cell production.
- General Motors is developing its Ultium battery platform in-house.
However, none of these companies currently match BYD’s level of end-to-end control. This makes BYD a model — and perhaps a warning — for legacy automakers.
Why Consumers Should Care About BYD
If you’re in the market for an EV, there are good reasons to consider a BYD vehicle:
- Affordability: BYD offers feature-rich EVs at prices often lower than Western brands.
- Reliability: Vertical integration means fewer parts issues and better quality control.
- Innovation: Blade batteries, advanced safety systems, and software integration are all BYD hallmarks.
- Sustainability: BYD’s full-stack clean energy approach extends beyond cars to include solar panels, battery storage, and public transit.
The Power of Building Your Dreams
BYD’s story is one of vision, discipline, and innovation. From a battery startup to a global EV powerhouse, it has rewritten the playbook on what it means to be a modern automaker.
Vertical integration isn’t easy, and it’s not without risk. But in a world where supply chains are fragile, competition is fierce, and consumers demand more for less, BYD’s model may be the most future-proof.
As the world shifts toward electric mobility, BYD’s in-house empire could very well be the blueprint for the next generation of sustainable transportation.
Whether you’re an investor, a car buyer, or just someone fascinated by the EV revolution, one thing is clear: the future is being built — and BYD is doing it from the inside out.